AIによる故障予測とは
AIによる故障予測とは、AIやIoTの技術を活用して異常を検知し、故障する前に対応する予知保全のひとつです。
製造業における設備保全は、予知保全を含めて大きく3つに分けられます。
- 予知保全:AIやIoT技術を用いて、故障する前に対応する
- 予防保全:一定期間ごとに点検・メンテナンスを行う
- 事後保全:故障が発生した後に対応する
従来は予防保全と事後保全が主流でしたが、技術の進歩により予知保全、つまり「AIによる故障予測」を導入する企業が増加しています。
AIによる故障予測のアプローチ方法2つ
AIによる故障予測には、2つのアプローチ方法があります。
- 教師あり学習
- 教師なし学習
なお教師なし学習方法は、さらに3つの手法にも分けられます。ひとつずつみていきましょう。
【方法1】教師あり学習
教師あり学習は、あらかじめ正解のデータをインプットし、与えられたデータと正解データを比較して予測をおこなう学習モデルです。
もともと正解となるデータがあるため、正解と不正解が明確な場合に利用できます。
たとえば、設備の温度が70℃を超えたら異常とする場合、正解データは「70℃以下」です。70℃を超えた時点でAIがアラームを発するため、故障する前に対応できます。
項目が温度だけ、装置の数が1台だけの場合は人間でも監視は難しくありません。
しかし、複数の項目と複数の台数を監視する場合は、多くの手間とコストがかかります。そのため、正解となるデータがある場合は、教師あり学習が効果的です。
【方法2】教師なし学習
教師なし学習は、データはあるものの、分類(正誤)を事前に付すことができない場合に、データのみでAIが学習し、自身で分類できるようにする学習モデルです。
教師なし学習は、さらに3つの手法に分けられます。
- SVDD
- PCA
- RPCA
ひとつずつ紹介します。
1.SVDD
SVDD(Support Vector Data Description)は、データの集合を小さな円で囲むように学習する手法です。主に異常検知や異常計測に使用されています。
データの次元を上げて分析しやすくするカーネル法を用いて、正常なクラスのデータが収まるデータ群を作成し、そのデータ群から外れるデータを検知します。
2.PCA
PCA(Principal Component Analysis)は、データ群の主成分を分析することで正常・異常を判断する主成分分析と呼ばれる手法です。主成分とはデータに含まれる要素のことで、PCAでは主成分ごとにグルーピングします。
PCAを行うことで、複数の要素を持つデータがより少ない主成分で表せるようになります。したがって、PCAによる故障予測は正常なデータを定め、そのデータ群から外れるデータを異常として検知可能です。
3.RPCA
RPCA(Robust Principal Component Analysis)は、主成分分析のひとつです。
通常のPCAは外れ値の影響を大きく受けますが、RPCAは異常なデータ(いわゆる外れ値)の影響を受けず、正確な分析ができます。そのため、異常検知や画像処理などに広く使われています。
AIによる故障予測の導入方法4ステップ
AIによる故障予測を導入する手順は、下記のとおりです。
- センサーの選定
- データの取得
- 学習
- 実装・運用
まず前段階として、現状の課題を把握し、どんな改善をするのか定めます。そして、それらに向けてどんなデータが必要か考えましょう。順番に解説します。
【ステップ1】センサーの選定
必要なデータを洗い出したら、データを取得するためのセンサーを選定しましょう。有効なデータを取得するためにもセンサーを選ぶ際は、種類やサンプリングレート、取り付け場所などを確認しなければなりません。
故障予測に必要とされるデータの例は、下記のとおりです。
- 振動値
- 設備温度
- 動作音 など
設備や想定される故障によって分析に必要なデータは異なるため、センサーを選ぶ際は目的に適しているかしっかりと確認しましょう。
【ステップ2】データの取得
センサーの選定などの準備が終われば、分析に必要なデータを取得します。この後の学習に使用するデータなので、十分な量のデータが必要です。
データを取得してみて、足りなければ以下の対策も検討しましょう。
- センサーの追加
- 外部データ・オープンデータの使用
- データ取得用の稼働
センサーの追加は、そのまま実装時にも活用できるため精度を高めたい場合にも有効です
【ステップ3】学習
データから学習を行う環境を整え、取得したデータを元に、設備の正常稼働時、故障時のデータの特徴を学習することで、AIを生成します。
AI生成時には大きく分けて2つのプロセスを実行します。
- トレーニングデータを用いた学習
- テストデータを用いた精度評価
テストデータは、学習に使用しなかったデータを使用します。評価により算出された精度を確認し、必要に応じてデータを追加するなどで精度向上を目指します。
【ステップ4】実装・運用
実装のステップでは、必要に応じて監視機器などとAIを連携させる構築を行います。これによりAIが設備の故障を予測した際に、アラートを発報することなどが可能です。
また日々蓄積される最新のデータを追加し、継続的に学習をかけることで「AIの精度維持・向上」につながります。定期的な精度確認、必要に応じた再学習といった運用が重要です。
故障予測の精度を高めるためにも、運用して得られたデータの追加や結果を受けての改善を繰り返していきましょう。
AIによる故障予測の注意点3つ
AIによる故障予測の注意点は、下記のとおりです。
- AI人材の確保が必要
- 導入、運用コストなどがかかる
- 継続的な分析・改善が必要
AIは比較的新しい技術なので、適切に扱える人材を確保しなければなりません。即戦力となる人材を採用するにしても、従業員を教育するにしてもコストが必要です。ひとつずつ見ていきましょう。
【注意点1】AI人材の確保が必要
AIによる故障予測を導入する際は、AIの知見を持った人材の確保が重要です。AIは専門性が高い分野なので、知識やスキルの浅い人材がモデルを作ったりメンテナンスをしたりするのは現実的ではありません。
したがって、即戦力となる人材を新規で雇用するか、従業員にAIの教育が必要です。
さらに、AIを運用する際は、管理に必要な人件費もかかります。
AIによる故障予測が順調に稼働すると、最終的には人件費を超える生産性アップが見込めますので長期的な視点での導入が重要です。
なお、「Prediction One」はAIに関する専門知識がなくても予測分析が可能なツールです。
AI分析ツールを利用したことがない事業者に向けて、無料トライアルを提供していますのでぜひお試しください。
【注意点2】導入、運用コストなどがかかる
AIを始めとするシステムを導入する際、場合によっては導入、運用コストががかかります。上記と同様に順調に稼働さえできるようになれば、長期的な視点で見ると大きな効果を期待できるものの、結果が出るまでに時間がかかるケースもあります。
ただし、
- 自社開発するか
- クラウドサービスを利用するか
- 市販されているアプリケーションを利用するか
などによっても費用は大きく異なるため、自社のリソースや予算を考慮して導入を検討するのがおすすめです。
また、AIを生成する上で必要になるデータ取得のために、追加でセンサーが必要になったり、改修が必要になったりするケースもあります。ハードウェア面でも費用を考慮しておきましょう。
【注意点3】継続的な分析・改善が必要
AIによる故障予測を運用するためには、継続的な分析と改善が欠かせません。
日々、新しいデータを投入し、分析、改善することでAIの精度が増し、より正確な故障予測が可能になります。
また、AIを導入する際は、まず1台の設備だけに絞ってスモールスタートするのがおすすめです。一気にすべての設備に導入すると分析・改善に大きな手間がかかるため、効率がよくありません。
まずは、1台の設備で効果を高めてから、ほかの設備・生産ラインに横展開しましょう。
AIによる故障予測の事例2選
AIによる故障予測の事例を紹介します。
- 故障予測を利用してダウンタイムの改善
- 水道管で発生する漏水予測
【事例1】故障予測を利用してダウンタイムの改善
自動認識ソリューションを開発しているサトーホールディングス株式会社では、以下の課題に対し、予測分析ツール「Prediction One」を導入しました。
- データ分析業務が属人化していた
- データ分類に多大な工数がかかっていた
現在は、製品の保守データを学習させ「どうしてその障害が発生したのか」など故障原因を予測しています。
もともとは従業員が手作業でデータを分類していましたが、AIが出した結果をジャッジするやり方に変わったことで、8〜9名で丸3日かかっていた業務が4名で2日ほどに削減されました。
また、当該部署に異動したばかりの従業員がすぐに分類業務を行えるようになり、属人化の解消にも成功しています。
【事例2】水道管で発生する漏水予測
水道管の漏水調査をおこなう水道テクニカルサービス株式会社は、水道管で発生する漏水予測やクライアントである学校の使用水量の予測に「Prediction One」を導入しました。
学校の使用水量に関して、決定係数0.84と高い精度のモデルを作成しています。過去のデータを用いて予測してみたところ、従来よりも早く漏水を検知できる見込みとなりました。
また、水道管の漏水発生予測は漏水履歴と管路データを用いて学習し、有効性を検証しています。こちらも従来の方法と比較して、効率的に漏水を発見できる可能性を証明できました。
まとめ:AIの故障予測を導入して安定した生産活動をおこなう
AIによる故障予測は、製造における予知保全のひとつで、故障前に異常を検知して対応する手法です。
AIの学習は教師データの有無によって、教師あり学習と教師なし学習のどちらかを実施します。
過去の故障時のデータがある場合は、そのデータを教師データとして学習し、生成されたAIにより将来の故障を予測できるようになります。
AIを導入することで、故障予測の属人化や多大な工数問題を解決することができますが、AI人材の確保や導入、運用コストがかかるうえ、高い効果を実現するためには継続的な分析・改善が欠かせません。
ただし、長期的に見れば高い費用対効果を期待できるため、1台の設備に対してAIで故障予測をするところから始め、うまくいきはじめた段階で横展開して、安定した生産活動を目指しましょう。
なお、AIによる予測分析ツール「Prediction One」は、製造現場でも活用できます。
不良品の検知や出荷数予測などを資料にまとめたので、ぜひダウンロードのうえご活用ください!
お役立ち資料をダウンロード
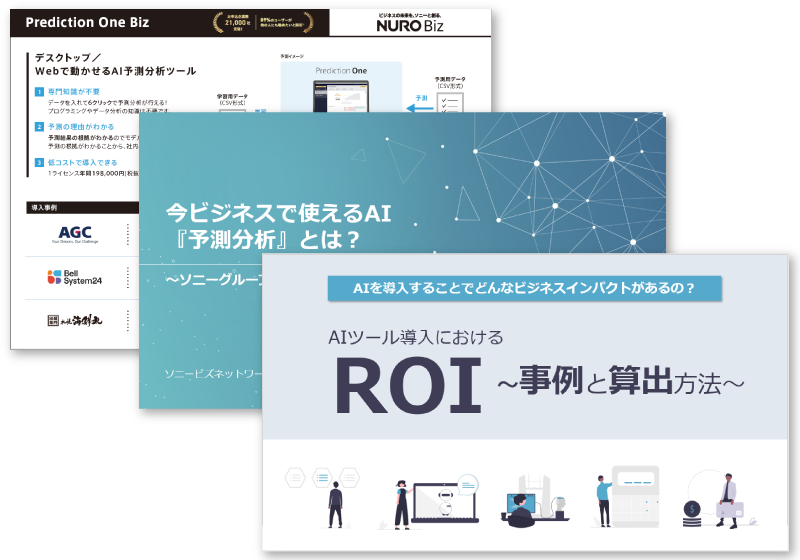
AI予測分析ツール「Prediction One」の概要やAI導入のメリットをまとめました。
■3つの資料わかること
・Prediction Oneとはどんなツールなのか?何ができるのか?
・予測分析をビジネス適用することによるビジネスメリットは?
・Prediction One導入企業の導入事例、ROI計算例