生産管理とは?
冒頭でもお伝えしたとおり、生産管理とは、製造業における生産計画に関わる業務全般を管理・最適化することです。業務の範囲は、需要予測や計画立案、原材料の購入、工程計画の作成・管理、品質管理などと多岐に渡ります。
生産管理と混同されがちなのが製造管理です。しかし、両者は同じ業務ではありません。
製造管理は、工程管理に特化した業務を指します。つまり、需要予測から品質管理まで全般的にカバーする「生産管理」と比べ、製造管理はより具体的なプロセスに焦点を当てているのです。
生産管理の目的
生産管理の主な目的は、利益の最大化です。
たとえば、製品の納期が遅れるとクライアントに迷惑がかかり、企業の信頼性や顧客満足度に影響を及ぼすリスクがあります。また、在庫の量が過剰または不足だと、資金繰りの悪化や販売機会の損失といった問題が生じかねません。
このようなリスクや問題を避けるため、計画で定められた数量の製品は期限までにつくる必要がありますし、在庫も適切な量を常に維持する必要があります。
製造業において重要な考え方は、「品質の良いものを(Q:Quality)、原価を抑えて(C:Cost)、短納期でつくる(D:Delivery)」という3つの要素(QCD)を最適化することです。
とはいえ、QCDをすべて一斉に最適化することは難しいもの。そこで、QCDのバランスや優先順位を決めることが、生産管理をするうえでのポイントとなります。
生産管理の重要性
製造業では、QCDの考えに基づき、高品質な製品を低価格かつ短納期で生産することが大切です。効率的な生産を行うためには、QCDを継続的に改善し続ける必要があります。
QCD(品質、コスト、納期)を最適化するためには、全体のプロセスをチェックし、ボトルネックを把握したうえで改善しなければなりません。
今後の製造業は、労働力の不足や設備の老朽化といった問題がより深刻化することが予想されています。また、ニーズの多様化にも対応していかなければなりません。
これらの課題や変化に対応し、製造ラインを持続的に最適化するためには、生産管理の役割はより一層重要です。
生産管理の工程について
生産管理の業務内容は、主に以下のように分類できます。
- 需要予測
- 生産計画
- 調達・購買計画
- 生産実施
- 工程管理
- 品質管理
- 在庫管理
それぞれ確認していきましょう。
需要予測
生産管理における需要予測とは、在庫リスクを減らすため、データや景気から受注量を予測するプロセスのことです。仕入れが少なすぎると機械損失になりますし、多過ぎても過剰在庫になるため、適性な在庫数を確保するために需要予測が必要になります。
需要予測を行う方法には、「実績やデータから需要量を予想する方法」と「従業員の勘を元に需要量を予測する方法」の2つがあります。
具体的な手法は以下の通りです。
- 算術平均法:複数の数値を平均して予測値を算出する方法
- 移動平均法:仕入れごとに商品単価の平均を算出する方法
- 指数平滑法:過去のデータから予測値を算出し、新しい予測値を算出する方法
- 回帰分析法:因果関係がある数値の関係性から需要を算出する方法
- 加重移動平均法:最新の需要変動の影響を加味して算出する方法
各手法については下記の記事で詳しく解説しているので、ぜひご一読ください。
生産計画
生産計画とは、製品の生産量や時期について計画を立てるプロセスです。
生産にかかる原材料・部品の数量や人員などを考慮しながら、製造から出荷までの日程を考える必要があります。調達や手配に時間がかかるケースもあるため、内的要因(生産能力や設備の稼働時間など)だけでなく、外的要因(市場の需要や原材料の供給状況など)も含めなくてはなりません。
生産計画の手法は、主に2通りあります。
- 引っ張り方式:顧客の受注量や納期に合わせて計画を立てる方法
- 押し出し方式:生産計画を立てたうえでスケジュール通りに進めていく方法
引っ張り方式は在庫が過剰に出にくいメリットはありますが、顧客の要望によってスケジュールがタイトになる場合も。一方押し出し方式は、計画通りに業務を進められますが、過剰在庫が出やすく無駄なコストが発生しやすいというデメリットがあります。
また、生産計画は大日程(3か月〜1年間)・中日程(1か月〜3か月)・小日程(1週間~1か月後)まで細分化していくのが一般的です。
大日程は全体の戦略や方針を定め、中日程では具体的な作業計画を、小日程では日々の作業スケジュールを決定するというイメージです。
細分化して生産計画を立てることで、より効率的かつ効果的な生産活動を実現できます。加えて、仮に大日程の計画から外れた場合や問題が発生した場合でも、中日程や小日程の計画を見直しすれば迅速に対応できます。
調達・購買計画
調達・購買計画とは、必要な原材料の調達や購買を計画するプロセスです。調達と購買は、必要なものを手に入れる目的は同じですが、その過程や範囲に違いがあります。
調達はより広い範囲をカバーしており、必要な商品やサービス(資金や労働力も含みます)を全体的に確保する過程です。必要な商品やサービスの特定から、必要な商品やサービスを供給するまでのプロセスが含まれます。
たとえば、オフィスに必要な備品をどこの業者から、何を、どれくらい、いくらで購入するか、など全体を考えて購入することです。
一方、購買は具体的な商品やサービスを買い入れることで、「オフィスのコピー用紙が無くなったので、新たに注文する」といった行為です。購買は調達の一部とも言えるため、限定的な言葉となります。
生産実施
生産実施は、生産計画と調達・購買計画に従って製造を開始するプロセスです。計画通りに実行し、生産ラインの効率を最大化します。
しかし、必ず計画通りに進められるとは限りません。自然災害の被害やクライアントの要望などが原因で、受注量が急遽変更される場合もあるため、イレギュラーなケースにも対応できるようにしておくことが大切です。
工程管理
工程管理とは、計画された目標と実際の進捗を比較し、そのギャップを特定し改善するプロセスです。「計画通りに生産が進んでいるか」「設備の使用率は問題ないか」などを管理します。
工程管理を実施すれば、各工程の製造状況を確認できるため、もしどのかの工程で不具合が発生しても早期に発見できます。
品質管理
品質管理とは、製品に一定の品質が備わっているかをテストして保証するプロセスです。製品に問題が見つかった場合は、その原因を特定し顧客へのクレームにも対応します。
品質管理の主な工程は、下記の3つです。
- 工程管理:各工程での検査を実施
- 品質検証:基準を満たした製品であるか確認
- 品質改善:不具合の原因特定からトラブル再発防止策検討など
品質管理の目的は、製品の原材料調達から市場流通までの範囲で、一定の品質を維持することです。そのため、不良品や不適合品が紛れ込まないように、リスクを考慮した管理が求められます。
以前は人間が目視で検査していましたが、最近では機械やAIに代用され始めました。AIを用いた品質管理の導入は特に注目されており、その詳細については以下の記事で解説しています。気になる人はぜひご覧ください。
在庫管理
在庫管理は、各製品ごとの在庫数を管理するプロセスです。在庫が不足していれば製造量を増やす必要がありますし、逆に在庫が過剰な場合は製造のペースダウンを検討します。
適切な在庫管理には、現在の在庫数を正確に把握し、その情報をもとに理想的な在庫状態を維持しなければなりません。在庫管理が適切に行われると、不必要な発注や過剰在庫を回避でき、結果的にコスト削減につながります。
生産管理の知っておきたい注意点について
生産管理は製造業にとって大切な業務ですが、以下のような注意点が存在します。
- リアルタイムに進捗確認ができない
- 担当者のスキルや経験でパフォーマンスが異なる
- 部門ごとに情報が異なるため一元化しにくい
- 設備や人員の負担状況を確認できない
- 原価計算が難しい
それぞれを確認しましょう。
リアルタイムに進捗確認ができない
作業日報を手動で作成している製造業では、日報の集計や確認に時間がかかります。その結果、現在の進捗状況をリアルタイムで確認できません。
「進捗が計画通り進行しているのか」「遅れがある場合にどの程度なのか」といった状況を把握できないと、対応が遅れてしまうリスクがあります。
また、部門間の連携が取れていない場合、他部門の進捗状況が把握できないことが要因となり、問題が生じやすいです。少なくとも、関連部門の進捗が全体的に見えなければ、全体の生産管理の最適化は難しくなります。
担当者のスキルや経験でパフォーマンスが異なる
生産管理は、担当者のスキルや経験に大きく依存していることが多いです。そのため、経験が豊富な従業員に業務が集中してしまい、負担が偏っている場合が多々あります。
また、「生産管理に関する具体的なマニュアルが社内に存在しない」「情報共有や教育の時間を十分に確保できていない」といった理由で、業務の属人化が起こっているケースも少なくありません。この問題については、以下の記事で詳しく解説しているので、ぜひご一読ください。
部門ごとに情報が異なるため一元化しにくい
製造業において、部門間でデータ連携ができずに生産管理に手こずるケースがよく見受けられます。各部門ごとに使用しているITツールが異なる、データの定義がバラバラといった状態では、一貫した生産管理が困難です。
さらに「どの情報が最新か?」といった基本的な認識のズレが生じてしまい、現場でのトラブルや品質不良の発生を引き起こす恐れがある点も注意しましょう。適切な生産管理のためには、各部門が連携しながら、生産過程を一元管理するのが理想です。
設備や人員の負担状況を確認できない
製造業における担当者のパフォーマンスは、個々のスキルや経験に左右される場合が多くあります。製造現場では特定の設備や人員へ負担が偏ることがよくあり、これらの負担は現場に直接立たないと捉えにくく、管理者が詳細に把握するのは難しいものです。
設備の過度な使用やスタッフの過労は、故障や人員の健康問題という重大な結果を招くリスクがあります。
原価計算が難しい
製品にかかった原材料費・人件費・設備費用といった原価は、実際に製造すると見積もりよりも高くなってしまう場合が多くあります。その理由は、原材料費の変動や人的なミス、試作品の作成などさまざまです。
また原価計算自体が複雑なプロセスであるため、正確に計算するにもハードルが高く結果として、赤字になってしまうケースも珍しくありません。
生産管理を効率化するツール導入がおすすめの理由
これまでに挙げた生産管理の注意点は、ツール導入によって解決可能です。本章では、生産管理においてツール導入がおすすめできる理由をご説明します。
- 情報の見える化につながるから
- 属人化を解消できるから
- 業務効率が改善するから
それぞれ解説していきます。
情報の見える化につながるから
生産管理業務は多くの部署や担当者が関わっており、情報が各所に散らばっているケースが少なくありません。このような状況は、情報管理を複雑にし問題を解決しづらくしています。
ツールを導入することで情報を一元管理でき、各部署や担当者がアクセス可能なプラットフォーム上で共有されます。そのため、全員が同じ情報に基づいて行動でき、問題をすぐに可視化することが可能です。問題解決のスピードを早めるだけでなく、「古い情報を見て作業を進めてしまった」というミスや誤解を防ぐのにも役立ちます。
属人化を解消できるから
担当者の経験やスキルによるパフォーマンスのバラつき、いわゆる「属人化」の問題は、ツールの導入により解消できます。なぜなら、情報が1か所に集約され、情報共有や引き継ぎがしやすくなるためです。
特にAIツールを導入すると、需要予測のような社員の経験に依存しやすい業務も、ツールを使って誰でも行えるようになります。
業務効率が改善するから
ツールを導入し蓄積されたデータを活用することで、各フローの業務を効率化できます。
また、ツールの設計が従業員に使いやすい仕様であれば、導入後の運用率が高まり業務効率が一段と上がるでしょう。
このように、
- 情報の見える化につながる
- 属人化を解消できる
- 業務効率が改善する
といった理由で、生産管理にはツールを活用するのがおすすめです。
たとえば、AIを活用した「Prediction One」は、データ分析と予測に基づいて生産計画を最適化でき、多くの製造業における生産管理の課題を解決します。機械学習やプログラミングなどのスキルがなくても使いこなせるツールですので、導入を検討してみてはいかがでしょうか。
まとめ:生産管理の効率化には特にAIツールがおすすめ
生産管理は製造業において欠かせない業務で、下記の業務内容が各々大切な役割を担っています。
- 需要予測
- 生産計画
- 調達・購買計画
- 生産実施
- 工程管理
- 品質管理
- 在庫管理
しかし生産管理には「進捗をリアルタイムに確認できない」「属人化が起きやすい」といった課題も多く、適切に管理できていないケースも少なくありません。そこで、生産管理における課題を解消する方法として、ツールの導入が挙げられます。
「Prediction One」なら、AIを活用し予測モデルの構築から分析まで、直感的に操作できます。特に「予測」という経験豊富な従業員に属人化しやすい業務を、高精度なAI予測によって誰でも行えるのは大きな特長です。製造業をはじめさまざまな場面でご活用いただいており、非公開の事例も用意していますので、ぜひご気軽にお問合せください。
お役立ち資料をダウンロード
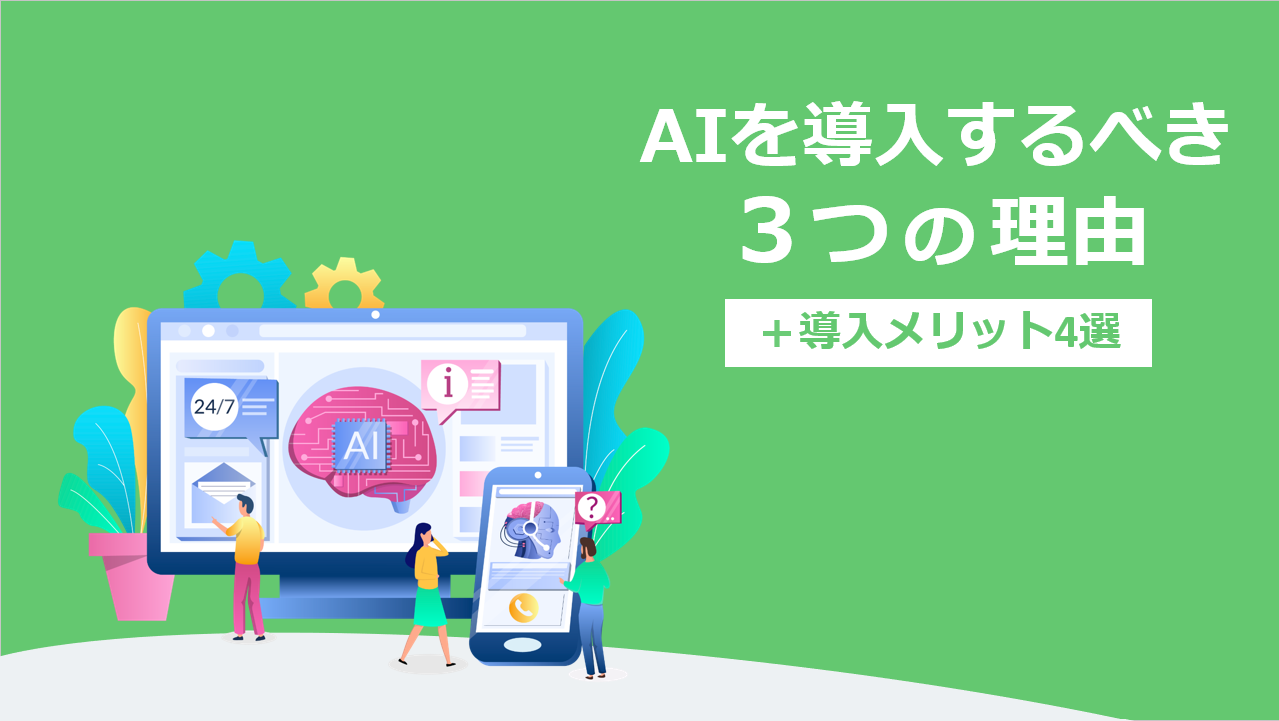
「AIを導入するべき3つの理由」のダウンロードをご希望のお客様は、
以下必要事項をご入力ください。